Introduction
This part of IsSO 15765 has been established in arder to define common requirements for vehicle diagnostic systems implemented on a Contolter Area Network (CAN) communication link, as specified in ISO 11898.Although primarily intended for diagnostic systems, it also meets requirements from other CAN-based systems needing a nowork layer pratocol.
To achieve this, it is based on the Open Systems Interconnection (OSI) Basic Reference Model specifred in ISOIEC 7498 and ISOI/IEC 10731, which strutures communication systems into seven layers. When mapped on this model, the servlces specified by ISO 15765 are divided into
-unifed diagnostic services (layer 7). specified in ISO 15765-3,
-network layer senvices {layer 3). specifed in ISO 15765-2,
-CAN services (layers 1 and 2). specifled in ISO 11898,
in accordance with Table 1.
The epplication layer services covered by Iso 15765-3 have been defined in compliance with diagnostic senvices established in ISO 14229-1 and ISO 15031-5. but are not limited to use only with them. ISO 15765-3 is also compatible with most diagnostic services defined in national standards or vehicte manufacturer's specifications.
The network layer services covered by ISO 15765-2 have been defined to be independent of the physical layer implemented, and a physical layer is onty specified for legislated OBD.
For other application areas, 1S0 15765 can be used with any CAN physical layer.
Table 1一Enhanced and leglslated-OBD diagnostic speciflcations aplicable to the OS1 layers
Open Systems Interconnection (OSI) layers |
Vehlele manufacturer enhanced diagnostics |
Legislated on-board diagnostics (OBD) |
Diagnostic application | User defined | ISO 15031-5 |
Applicason layer | ISO 15765-3 | ISO 15031-5 |
Presentation layer | N/A | N/A |
Session layer | ISO 15765-3 | N/A |
Transport layer | N/A | N/A |
Network layer | ISO 15765-2 | ISO 15765-4 |
Data link layer | ISO 11898-1 | ISO 15765-4 |
Physical layer | User defined | ISO 15765-4 |
1SO 15765-4:2005(E)
6 Network layer
6.1 General
The network layer of the exteral test equipment and the legislated-OBD compliant vehicle ECU(S)一from the external test equipment point of view 一shali be in accordance with ISO 15765-2 and the restrictions/additions givenin 6.2 to 6.4.
6.2 Addressing formats
For legislated-OBD communication, only the normal addressing format 一in the case of 11 bit CAN identifiers一and only the normal fixed addressing format- in the case of 29 bit CAN identifiers - as they are defined in ISO 15765-2, shall be used.
6.3 Data link layer interface
6.3.1 CAN identifer requirements
6.3.1.1 External test equipment
The exteral test equiprent shall support 11 bit and 29 bit CAN identifiers for legislated-OBD communication, for which it shall only accepl CAN identifiers which fit into the defined legislated-OBD CAN identfier ranges for 11 bt or 29 bit CAN identifiers (see 6.3.2).
For legislated OBD communication flowing the itlaliation sequence, the external test equipment shall only use 11 bit or 29 bit CAN identifers.
6.3.1.2
Legislated-OBD ECU
A legislated-0BD-compliant vehicle shall use a single CAN identifier size: either 11bit or 29 bit. From the external test equipment point of view, each legislated-O8D ECU in a given legislated OBD-compliant vehicle shall support either 11 bit or 29 bit CAN identifters ftor legislated-OBD request and response messages, support one pair of physical request and response CAN identifiers in accordance with 6.3.2,accept the functional request CAN identifer of the supported CAN identifier set (11 bit or 29 bit - see 6.3.2) for functionally addressed legislated-OBD request messages, and accept the physical request CAN identfier associated with the physica! response CAN identfier for physically addressed Flow Control frames sent by the external lest equipment (see 6.3.2)
6.3.2 Mapping of diagnostic addresses
6.3.2.1 Legislated-OBD CAN identifiers
The fllowing subclauses specity the 11bit and 29 bit CAN identifers to be used for legislated-0BD diagnostics. Both sets of CAN identifiers represent the mapping of diagnostic addresses into CAN identifers as follows. Table 2 defines the diagnostic addresses versus type of CAN identifier, whether physical or functional. For 11 bit CAN identifers, the mapping of the target address (TA) and source address (SA) into a CAN identifer is implied. Table 3 specifies the 11 bit CAN identifers to be used for legistated OBD diagnostics.
See Figure 6.
Table 2一Definition of diagnostic addresses versus type of CAN identifer
CAN identifier | Target Address (TA) |
Source Address (SA) |
TA type (TAtype) |
Message type (Mtype) |
Funclonal request | Legislated OBD system = 33 hex | External test equipment= F1 hex | functional | diagnostics |
Physical response | External test equipmentzF1hex | Legislated-OBD ECU=xx hex | physical | diagnostics |
Physical request | Legislated QBD ECU = xx hex | External test equipment= F1 hex | physical | diagnostics |
xx hex: ECU physial diagncstic adcress | ||||
NOTE: For delalled desciplions of parameters TA. SA, TAtype and Mttype. see 1SO 15765-2. |
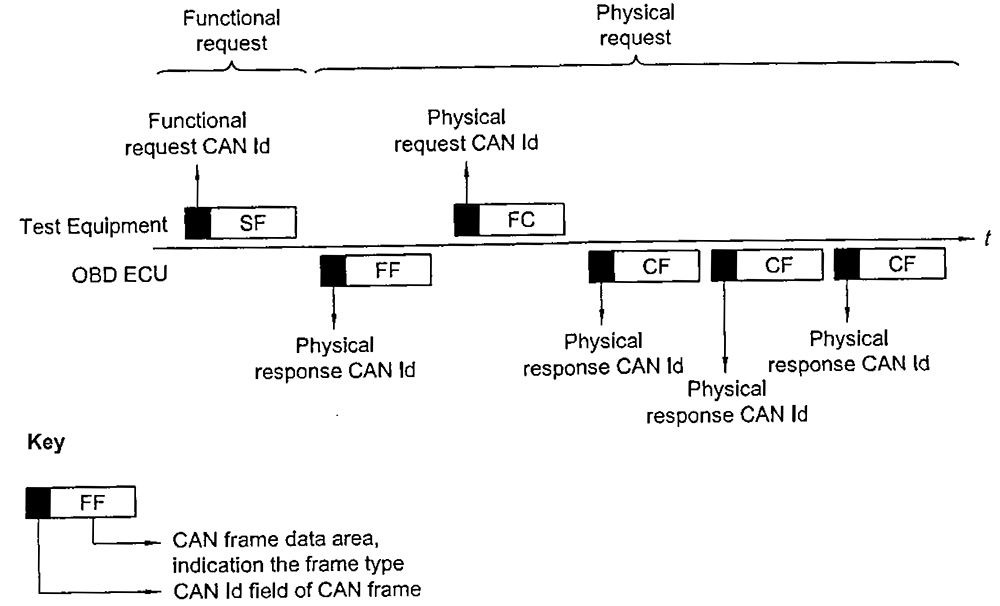
Figure 6一CAN identlfier usage
For legislated OBD:
- thefunctional request CAN identifier shall be used for functionally addressed request messages sent by the extemal test euipment,this particular CAN identifier representing the TA 33 hex (legislated-OBD functional system) and SA F1 hex (external test equipmenl);
- the physica! response CAN Id shall be used for physically addressed response messages sent by the legislated-OBD ECU(s), this particular CAN identifier representing TA F1 hex (extemal test equipment) and the physical diagnostic address (SA) of the ECU(s).
- the physical request CAN Id shall only be used for physically addressed FlowControl frames sent by the external test equipment, this particular CAN identifier representing the physical diagnostic address (TA) of the ECU and SA F1 hex (external test equipment).
The server identifer (physical diagnostic address) of a legislated-OBD ECU shall be unique to a given legislated-OBD-compliant vehicle.
The CAN identifiers specified for legislated OBD may also be used for enhanced diagnostics jif this usage does not interfere with legislated OBD.
6.3.2.2 11 bit CAN identifiers
Table3 specifies the 11 bit CAN identifers for legislated 0BD, based on the defined mapping of the diagnostic eddresses.
Table 3- 11 bit legislated-OBD CAN identifiers
CAN identiffer (hex} |
Description |
7DF | CAN identifer for functionally addressed request messages sent by exlemal test equipment |
7E0 | Physical request CAN identifier from external test equipment to ECU#1 |
7E8 | Physical response CAN identifier from ECU # to extemal test equipment |
7E1 | Physical request CAN identifier from extemal test equipment to ECU#2 |
7E9 | Physical response CAN identifler frorm ECU #2 to extemnal test equipment |
7E2 | Physical request CAN identiter lrom external test equipment to ECU *3 |
7EA | Physical response CAN identifier from ECU #3 1o external 1est equipment |
7E3 | Physical request CAN identer from extemai test equipment to ECU#4 |
7EB | Physical response CAN identifer ECU #4 to the external test oquipment |
7E4 | Physical request CAN identifer t:om external test equiprment to ECU #5 |
7EC | Physical response CAN ientifier from ECU #5 to exlernal 1est equipment |
7E5 | Physical request CAN identifier from extemal test equipment to ECU#6 |
7ED | Physical response CAN identfier from ECU #6 to external test equipment |
7E6 | Physical request CAN identifier from external test equipment to ECU #7 |
7EE | Physical response CAN identifier from ECU #7 to extemal test equipment |
7E7 | Physical request CAN identifier from external test equipment to ECU #8 |
7EF | Physical response CAN identifer from ECU#8 to external test equipment |
While not required for current implementations, it is strongly recommended (and may be required by applicable gislation) that for Iuture Implementaions the tllwing 11-bit CAN identifer assignments be - 7E0/7E8 for ECM (engine contro module); - 7E1/7E9 for TCM (transmission control module), |
6.3.2.3 29 bit CAN idontifiers
Tables4 and 5 specify the 29 bit CAN identifiers for legislated OBD, based on the defined mapping of the diagnostic addresses. The 29 bit CAN identifiers shall comply with the normal fixed addressing format acording to ISO 15765-2, summarized in Table 4.
Table 4 - - Summary of 29 bit CAN identifier format一Normal fixed addressing
CAN ld bit position | 28 | 27 | 26 | 25 | 24 | 23 | 22 | 21 | 20 | 19 | 18 | 17 | 16 | 15 | 14 | 13 | 12 | 11 | 10 | 9 | 8 | 7 | 6 | 5 | 4 | 3 | 2 | 1 | 0 |
Functional CAN id | 18 hex | DB hex | TA | SA | |||||||||||||||||||||||||
Physlcal CAN id | 18 hex | DA hex | TA | SA | |||||||||||||||||||||||||
NOTE: The CAN identilier values given In this table use the default value for the priority informalion in accordance with ISO 15765-2. |
Table 5一29 bit leglilated-OBD CAN identifiers
CAN ldentifier (hex) |
Descrlption |
18 DB 33 F1 | CAN identifier for functinally address request messages sent by extemal test equipment |
18 DA xx F1 | Physical request CAN lentifir from extemal lest equipment to ECU #xx |
18 DA F1 xx | Physical response CAN identifer from ECU #x to extemal test equipment |
The maximum number of legislated-0BD ECUs in a legislated-OBD- compliant vehicle shall not exceed eight (8). The physical ECU diagnostic address of an ECU (xx’hex) embedded in the physical CAN identiflers shallt be unique for a legislated-OBD ECU in a given vehicle.
While not required for current implementations, it is strongly recommended (and may be required by applicable legislation) that for future implementations the physical ECU addresses according to the assignments found in SAE 32178/1.
6.4 Network layer parameters
6.4.1 Network tayer timing parameter values
Table 6 specifies the network layer timing parameters to be used by the external test equipment and the legislated-OBD-complant vehicle- from the external test equiprment point of view - for legislated-OBD communication.
The listed performance requirement values are the binding communication requirements for the external test equipment and the legislated-OBD ECU(s) considered as being legislated-OBD-compliant. The timeout values are defined to be higher than the values for the pertommance requiements in order to overcome communication conditians where the performance requirement absolutely cannot be met (owing to external conditions such as high bus load).
Table 6一Network layer timeout and performance requirement values
Parameter | Timeout value | Performance requirement value |
N_ As/N_Ar | 25 ms | - |
N_Bs | 75ms | - |
N_Br | - | (N_Br+N_Ar)< 25 ms |
N_ Cs | - | (N_ Cs+N_As) < 50 ms |
N_ Cr | 150 ms | - |
Owing to aplication layer timing requirements, the floving performance requrement for the transmission of a single or first frame of an ECU response message applies: P2CAN.ECU+N_As≤P2CANmax |
||
NOTE 1 : For a detaled description of the network layer timing parameter velues, see 1s0 15765-2. NOTE 2 : For a detbiled desrption of the apllcation layer uiming panameler P2, see Iso 15031-5. |
6.4.2 Definition of external test equipment network layer parameter values
The external test equipment shal use the following network layer parameter values for its FlowControl frames sent in response to the reception of a FirstFrame. See Table 7.
Table 7 - - External test equlpment network layer parameter values
Parameter | Name | Value | Description |
N_WFTmax | WaitFrame Transmission |
0 | No FlowControl wait frames are alloweld for legislated OBD. The FlowControl frame sent by the extemal test equlpment following the FirstFrame of an ECU response message shall Contain the Flowstatus FS set to 0 (ClearToSend),which forces the ECU to start immediately after the reception of the FlowControl frame with the transmission of the ConsecutiveFrame(s) |
BS | BlockSize | 0 | A single FlowControl frame shall be transmitted by the external test equipment for the duration of a segmented message transfer. This unique FlowControl frame shall follow the FirsiFrame of an ECU response message. |
STmin | SeparationTime | 0 | This value allows the ECU to send ConsecutiveFrames, followlng the FlowControl frame sent by the extemal test equlpment, as fast as possible. |
If a reduced Implementation of the ISO 15765-2 network layer is done in a legislated-OBD ECU, covering only the above listed FlowControl frame pararmeter values (8S,STmin). then any FlowControl frame received during legislaled-OBD cormmunlcation and using different FlowControl frame parameter values as defined in this table shall be ignored by the receiving legislated-OBD ECU (treated as an unknown network layer protocol data unit) |
6.4.3 Maximum nunmber of leg!slated-OBD ECUs
The maximum number of legislated-OBD related ECUs In a vehicle shall not exceed eight (B). The network layer of the extemal test equipment shall be capable of receiving segmented data from eight (8) legislated-OBD ECUs in parallel.